Dmitry Yakovlev
Posts
Process Structure
Design management
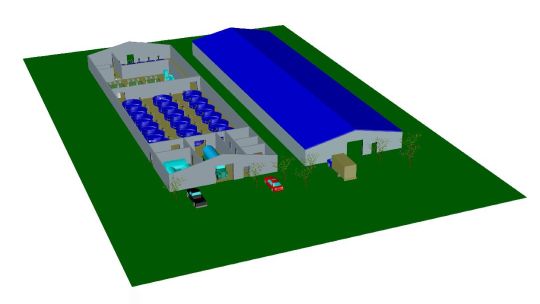
What constitutes the design process? To tackle any intricate procedure effectively, it should initially undergo decomposition, breaking it down into its most fundamental components. The process of designing a novel aquaculture facility can be categorized into the following sequential steps:
Guide
HOW TO START A FISH FARM

Choosing technology for trout farming
Safety factors
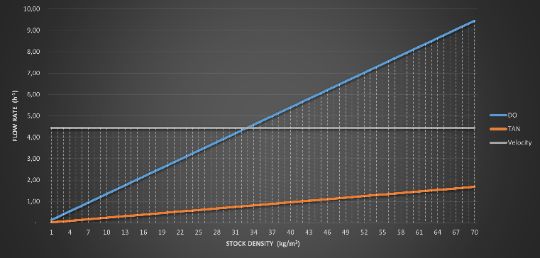
However, the picture changes significantly when factors appear that destabilize the normal operation of flow-through facilities.

How to start a fish farm
The simplest and most detailed guide on how to start a fish farming business and open a fish farm:
1. Start with Market Research:
a. Determine the fish species in demand
b. Identify the current sources of the desired fish species
c. Analyze the aquaculture technology of competitors (this will help estimate their production costs)
d. Assess the potential competition
e. Determine the market capacity.
2. Select a Suitable Location:
a. Ensure there is a sufficient source of high-quality water
b. Check for infrastructure for wastewater disposal
c. Confirm the availability of electricity
d. Consider gas supply (if required for your region and fish species)
e. Ensure accessibility for staff
f. Evaluate logistical access.
3. Verify Legal Requirements for the Chosen Location:
a. Obtain government permits for your type of business.
b. Confirm land use regulations.
c. Ensure there are no potential conflicts with environmental organizations, etc.
4. Decide on the Fish Species, Productivity, and Resources.
Obtain a commercial proposal.
5. Establish a Legal Entity.
6. Purchase or Lease Land for the Farm.
7. Plan the Design of the Aquaculture Farm:
a. Find a technology designer.
b. Locate a general contractor.
8. Obtain Building Permits (after developing project documentation).
9. Commence Construction.
10. Organize Equipment Procurement.
11. Coordinate Equipment Installation.
12. Conduct Commissioning and Startup Activities.
13. Legally Put the Facility into Operation.
14. Develop Standard Operating Procedures (SOPs).
15. Hire and Train Personnel.
16. Stock the Fish.
17. Arrange Consulting for the Initial Operation Period.
Some tasks can be performed simultaneously, while others need to follow a specific sequence. To manage the project efficiently, a project manager can create a Gantt chart.
You can either hire project management services to oversee the entire project or engage in specific tasks related to design, support, and more.
© Dmitry Yakovlev
Design management. Process Structure
What constitutes the design process? To tackle any intricate procedure effectively, it should initially undergo decomposition, breaking it down into its most fundamental components. The process of designing a novel aquaculture facility can be categorized into the following sequential steps:
1. Conceptualization of the Entire Enterprise:
- Crafting a comprehensive concept for the entire operation.
- Developing a production flowchart.
- Conducting calculations for key technological parameters and determining the necessary spatial requirements.
- Preliminary planning of the building's configuration.
- Identifying the optimal placement within the facility's grounds.
- Subdividing the building into distinct workshops. Frequently, this phase is executed during the proposal stage.
2. Development of Primary Workshops:
Performing technological calculations.
Creating a workflow diagram for each workshop.
Selecting appropriate equipment.
Arranging tanks and configuring the workshop layout.
Installing Recirculating Aquaculture System (RAS) equipment and designing reservoirs within the workshop.
3. Designing a Makeup Water Treatment Facility
4. Designing Utility Spaces:
- Designing technical rooms, locker rooms, bathrooms, administrative spaces, and other necessary amenities. Depending on the facility's scope, additional spaces like fish processing areas, ventilation chambers, and heating points may also be included.
5. Synthesizing Solutions into a Comprehensive Facility Configuration:
- At this juncture, it is possible to revisit previous stages to ensure alignment among the decisions made.
- All decisions are made in compliance with applicable standards.
- Project documentation, known as the Basic Design, is generated upon the completion of this stage.
This structured approach ensures that the design process for an aquaculture facility is methodical and comprehensive, meeting the necessary standards and requirements.
© Dmitry Yakovlev
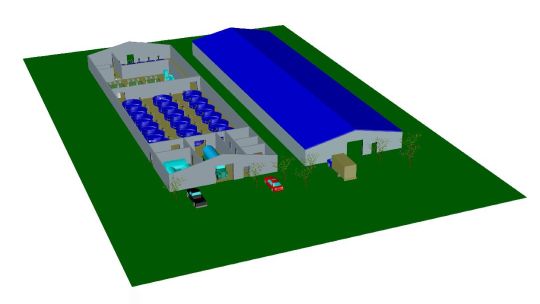
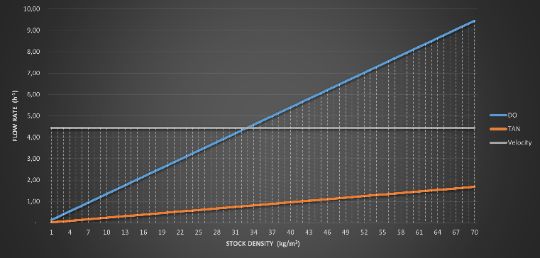
Choosing technology for trout farming
Safety factor, independence from weather conditions.
Competing with natural conditions is always a useless exercise for technical systems.
If we take trout farms located in mountainous regions with natural clean water, in most cases they have free water resources and not a RAS can compete with such a farm in terms of cost.
However, the picture changes significantly when factors appear that destabilize the normal operation of flow-through facilities. For example, in mountainous areas with clay or black soil, the turbidity of the water increases significantly during the rainy season. The fish stops eating normally (does not see food), the gills become clogged, immunity decreases, and the level of diseases increases. In such cases, there is a need to use additional technological solutions.
Using the example of one of the trout farms, a technical and economic analysis was made to choose the path for its modernization.
To begin with, a mathematical model of the dependence of water consumption on planting density was built.
Water exchange was determined according to 3 criteria:
- the required dissolved oxygen level
- the maximum concentration of TAN
- the flow velocity.
From the graph it became clear that the dissolved oxygen level and flow velocity have the greatest influence. At the intersection of these trend lines is the optimal planting density.
Based on the model, the 3 most optimal modernization paths were identified:
1. Flow-through system with a stocking density of 30 kg/m3 - at the intersection of oxygen requirements and flow speed. Water supply in normal mode is 4 time per hour (h-1). During the period of turbid water, the water supply can be reduced by approximately 4 times until the maximum permissible concentration according to TAN is reached - 1 mg/l. Mechanical filters with a 10-micron screen are installed for this mode. At the same time, oxygen supply is additionally organized.
2. Semi-closed system. All input water passes through filters, with a constant water exchange rate of 1 time per hour. Inside the system, the water is circulated through the tanks 4 times, while being saturated with oxygen, which allows the planting density to be increased to 41 kg/m3
3. RAS. Daily water exchange is 20%. All input water is filtered through 10-micron mechanical filters and undergoes UV sterilization. There are 2 independent RAS systems inside, providing 4x water exchange in the tanks and a stocking density of 80 kg/m3.
Multiobjective optimization included, factors such as:
- annual productivity (t/y)
- increase in annual productivity (as a result of modernization)
- capital expenditures (capex)
- capex per 1 ton of products produced per year
- capex for productivity increase 1 ton per year
- hourly electricity consumption
According to the results, the most effective technology turned out to be the closest to natural technology – option 1, filtration during the period of turbidity with oxygen supply.
Capex for 1 ton of products produced per year are $2.47 /t
0 additional kWh (0.3 kWh/t with filtration)
Option 2
Capex per 1 ton of products produced per year are $2.93 /t
Specific hourly electricity consumption is 0.52 kW h/t – in normal mode, 0.73 kW h/t during filtration
Option 3
Capex per 1 ton of products produced per year are $3.74 /t
Specific hourly electricity consumption is 0.93 kWh/t
At the same time, non-numeric criteria (security level, uniformity of capacity) in this case also indicated the effectiveness of Option 1.
Thanks for reading the article!
If you have any questions, write in a way convenient for you: CONTACTS
© Dmitry Yakovlev